W procesie obróbki skrawaniem każda zmiana kształtu, wielkości, położenia i charakteru przedmiotu produkcyjnego, tak aby stał się on produktem gotowym lub półproduktem, nazywana jest procesem obróbki mechanicznej.
Proces obróbki można podzielić na odlewanie, kucie, tłoczenie, spawanie, obróbkę skrawaniem, montaż i inne procesy. Mechaniczny proces produkcyjny ogólnie odnosi się do części procesu obróbki i procesu montażu maszyny.
Sformułowanie procesu obróbki mechanicznej musi określać przedmiot obrabiany, który ma przejść przez kilka procesów oraz kolejność procesu, podaje jedynie nazwę głównego procesu i jego sekwencję przetwarzania w krótkim procesie, znaną jako trasa procesu.
Sformułowanie trasy procesu polega na sformułowaniu ogólnego układu procesu procesowego, głównym zadaniem jest wybór metody obróbki każdej powierzchni, określenie kolejności obróbki każdej powierzchni oraz numeru całego procesu. Formułowanie trasy procesu musi być zgodne z pewnymi zasadami.
Zasady projektowania trasy technologicznej części obrabianych:
1. Pierwszy punkt odniesienia obróbki: części będące w procesie obróbki, jako powierzchnia odniesienia pozycjonowania, powinny zostać poddane obróbce w pierwszej kolejności, aby jak najszybciej zapewnić dokładne dane do przetwarzania w kolejnym procesie. Nazywa się to „najpierw benchmarkingiem”.
2. Podzielony etap przetwarzania: wymagania jakościowe przetwarzania powierzchni są podzielone na etapy przetwarzania, ogólnie można je podzielić na obróbkę zgrubną, półwykańczającą i wykańczającą trzy etapy. Głównie w celu zapewnienia jakości przetwarzania; Sprzyja racjonalnemu wykorzystaniu sprzętu; Łatwy do zorganizowania proces obróbki cieplnej; A także ułatwić wykrywanie pustych defektów.
3. Pierwsza powierzchnia po otworze: w przypadku korpusu skrzyni, wspornika i korbowodu oraz innych części należy poddać obróbce otwór obróbczy w pierwszej płaszczyźnie. W ten sposób otwór do obróbki pozycjonowania płaszczyzny zapewnia dokładność położenia płaszczyzny i otworu, ale także na płaszczyźnie obróbki otworu, aby zapewnić wygodę.
4. Obróbka wykańczająca: Główna obróbka wykańczająca powierzchni (taka jak szlifowanie, honowanie, szlifowanie dokładne, walcowanie itp.) powinna znajdować się na ostatnim etapie procesu, po obróbce wykończenia powierzchni w Ra0,8 um powyżej, niewielka kolizja uszkodzi powierzchnię, w krajach takich jak Japonia, Niemcy, po zakończeniu obróbki flanelą, absolutnie nie ma bezpośredniego kontaktu dłonią z obrabianym przedmiotem lub innymi przedmiotami, aby chronić wykończone powierzchnie przed uszkodzeniami w wyniku przeładunku i montażu pomiędzy procesami.
Inne zasady projektowania trasy technologicznej części obrabianych:
Powyżej przedstawiono ogólną sytuację organizacji procesów. Niektóre szczególne przypadki można rozwiązać zgodnie z poniższymi zasadami.
(1) Aby zapewnić dokładność obróbki, obróbkę zgrubną i wykańczającą najlepiej wykonywać oddzielnie. Ze względu na obróbkę zgrubną ilość skrawania jest duża, przedmiot obrabiany pod względem siły skrawania, siły docisku, ciepła i powierzchni obróbki ma bardziej znaczące zjawisko utwardzania przez zgniot, występuje duże naprężenie wewnętrzne przedmiotu obrabianego, jeśli obróbka zgrubna i zgrubna jest ciągła, precyzja wykończenia części zostanie szybko utracona z powodu redystrybucji naprężeń. Do niektórych części o dużej dokładności obróbki. Po obróbce zgrubnej i przed wykańczaniem należy przeprowadzić proces wyżarzania lub starzenia w niskiej temperaturze, aby wyeliminować naprężenia wewnętrzne.
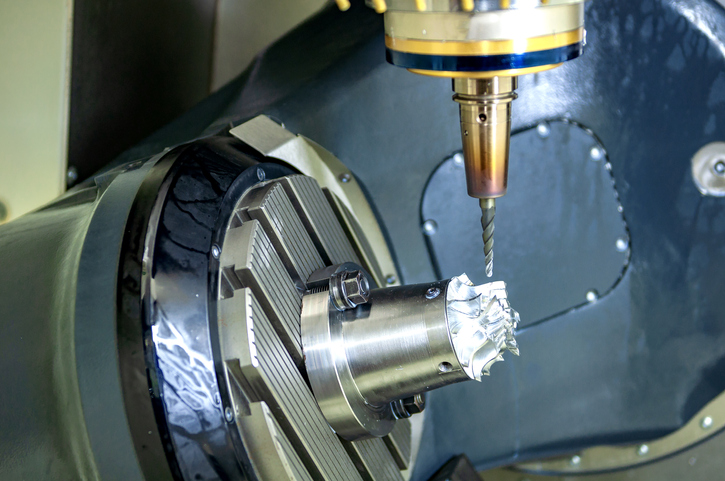
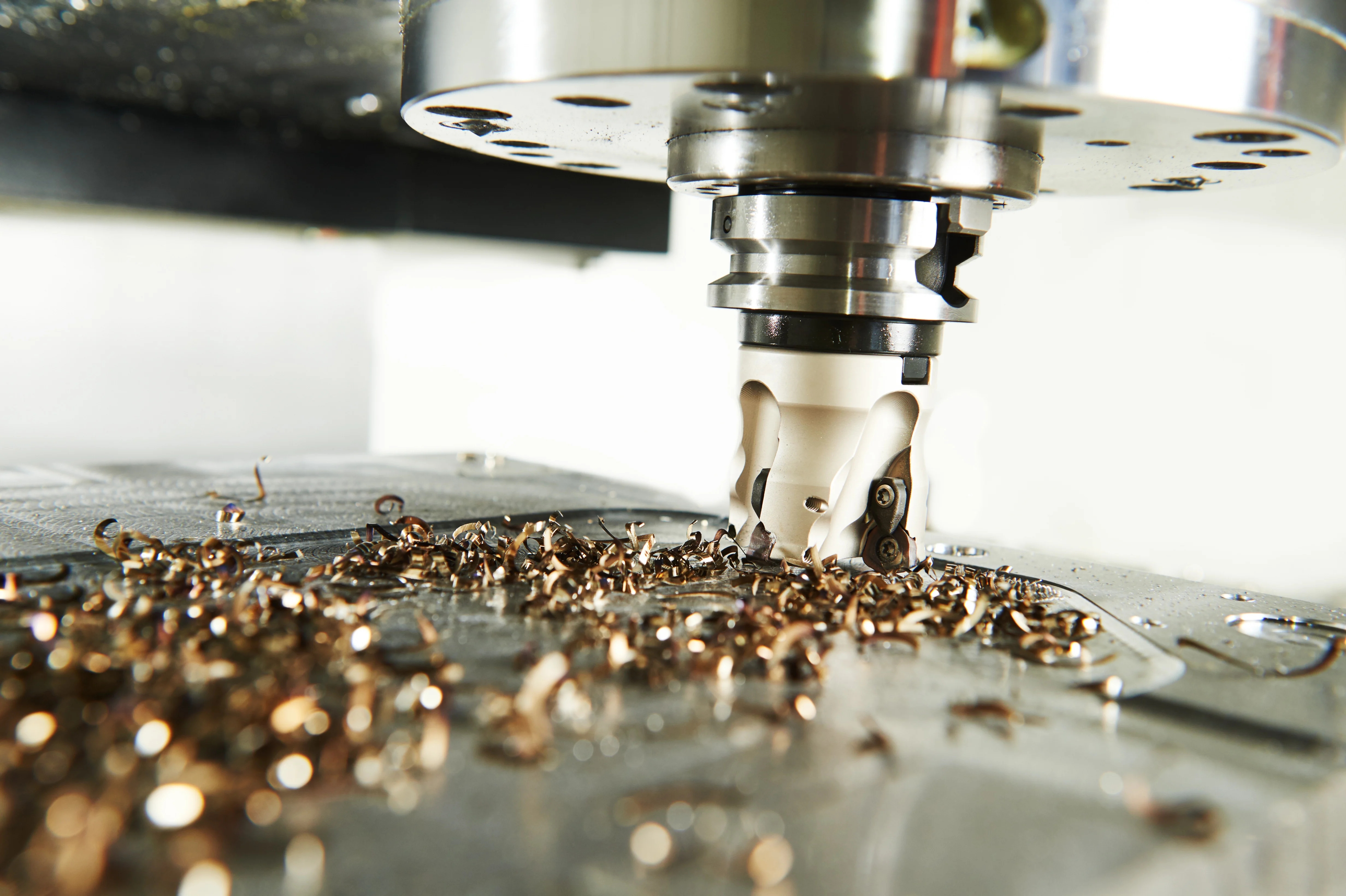
(2) Proces obróbki cieplnej często łączy się z procesem obróbki mechanicznej. Pozycje procesów obróbki cieplnej są rozmieszczone w następujący sposób: w celu poprawy obrabialności metali, takich jak wyżarzanie, normalizowanie, hartowanie i odpuszczanie itp., zazwyczaj przeprowadza się je przed obróbką. Aby wyeliminować naprężenia wewnętrzne, takie jak obróbka starzenia, hartowanie i odpuszczanie, ogólne ustalenia po obróbce zgrubnej, przed wykończeniem. W celu poprawy właściwości mechanicznych części, takich jak nawęglanie, hartowanie, odpuszczanie itp., Zwykle przeprowadza się je po obróbce mechanicznej. W przypadku obróbki cieplnej po większym odkształceniu należy również zorganizować proces końcowego przetwarzania.
(3) Rozsądny wybór sprzętu. Obróbka zgrubna ma głównie na celu odcięcie większości naddatku na obróbkę, nie wymaga większej dokładności obróbki, więc obróbka zgrubna powinna odbywać się z większą mocą, precyzja na obrabiarce nie jest zbyt duża, proces wykańczający wymaga obrabiarki o większej precyzji przetwarzanie. Obróbka zgrubna i wykańczająca jest przetwarzana na różnych obrabiarkach, co może nie tylko zapewnić pełną wydajność sprzętu, ale także wydłużyć żywotność precyzyjnych obrabiarek.
Podczas opracowywania procesu obróbki części, ze względu na różne rodzaje produkcji części, sposób dodawania, wyposażenie obrabiarek, zaciskanie narzędzi pomiarowych, półfabrykat i wymagania techniczne dla pracowników są bardzo różne.
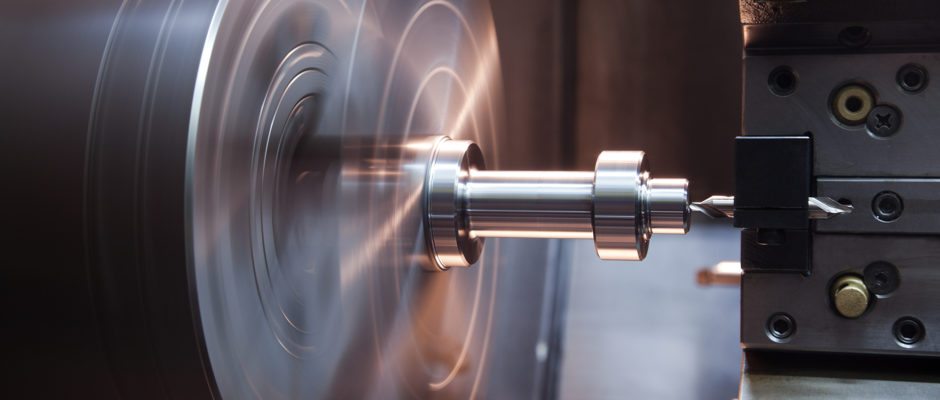
Czas publikacji: 23 sierpnia 2021 r